American Plastic Molds are a crucial part of the manufacturing process. They are used to shape and create multiple copies of the desired product or part.
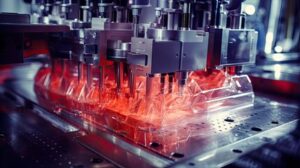
A plastic injection mold can take several weeks to design, build and produce. It is also expensive compared to 3D printing and CNC machining.
The type of plastic mold you need depends on the product or part’s shape, specifications, and use. These factors determine the process used to create the mold, which in turn affects the quality of the finished product. The five main types of plastic molding are extrusion, compression, blow, injection and rotational molds.
Regardless of the type of plastic you choose, it is important to select the best possible material to ensure optimal results. This will help to improve the overall quality of your product and reduce costs by minimizing waste. The best material for your project may vary depending on its requirements, but a few of the most common options include polyethylene (PE), polypropylene (PP), polystyrene (PS), and high-impact polystyrene (HIPS).
Injection molding is a fast and efficient way to produce plastic parts with complex shapes and precise dimensions. It is also an ideal choice for manufacturing parts that will require metal or non-metal inserts. The injection molding process heats the plastic to a molten state and then injects it into the mold cavity under high pressure. Once cooled, the molded product is removed from the mold. This is a cost-effective option for producing large quantities of plastic products and can be adapted to a variety of different industries.
Unlike 3D printing, which produces a single part at a time, injection molding requires the creation of multiple identical molds. For this reason, it can take up to 16 weeks for a production run to begin after the initial tooling phase. To minimize this timeline, it is a good idea to consult with an experienced manufacturer early in the design process. This will help you avoid falling into common pitfalls that can set your project back weeks and thousands of dollars.
This type of plastic molding begins with a pre-hardened, corrosion-resistant steel that is heat treated to achieve the desired surface hardness and mechanical properties. It is suitable for companies that need durable, long-lasting plastic products that will withstand a range of temperature conditions and environmental stresses. It is also a useful option for making hollow products, such as hoses and piping, as well as molded plastic shells.
Continuous Moulding
Unlike sand casting, which uses molds that have to be created one at a time for each individual bar needed, continuous cast metal is a more efficient method that eliminates the need for repulping the mold after each batch. This helps to reduce the number of stops and increases production speed, resulting in savings on material and labor costs.
The process of continuous casting also offers other benefits such as improved product quality, reduced machining needs, and lower manufacturing costs. The controlled cooling of the casting mold leads to a more uniform microstructure in the metal, reducing defects such as porosity and segregation. Moreover, the consistent cross-sectional dimensions of continuous-cast metal products make them easier to process and machine, further reducing machining expenses.
Once the molten graphite is ready to be shaped, it’s transferred from the tundish to the casting molds. The casting molds are typically constructed from isostatic graphite, a high-performance material with excellent mechanical properties and thermal and oxidation stability. Graphite is also self-lubricating, which minimizes contact friction between the molten graphite and the mold, avoiding deformation.
The molds are designed to control the flow of the molten graphite, and they are equipped with heating belts that help to keep them at the correct temperature as they enter and leave the casting zone. They are also designed to minimize buckling and distortion due to thermal expansion, particularly when casting wide strips.
After the casting, the molten graphite is cooled in a secondary cooling zone. The graphite is cooled using water sprays or air mist, which ensures that it does not stick to the mold walls when solidifying. This method also helps to prevent the formation of surface imperfections and defects such as slag, pitting, and streaking.
The resulting strand of solidified graphite is withdrawn at a constant rate from the bottom of the mold, and it passes through several cooling zones to refine its microstructure and improve mechanical properties. The strand is then cut into pieces that are coiled or transferred for further processing, depending on the application. The continuous-casting process can be used to produce a variety of products, including rods and blocks for crucibles and electrodes.
Short Run Moulding
Short-run injection molding is a manufacturing process that produces finished plastic parts in small batches. Its rapid turnaround times and flexibility make it a popular choice for testing new designs and products. It is particularly suited for entrepreneurs and inventors looking to develop and market their ideas while minimizing upfront costs and liability associated with large-quantity production.
Unlike traditional plastic injection molding, which uses complex steel molds, the molds used in short-run production are often made of aluminum. This is because the latter is a much easier material to manufacture and machine, and it can also withstand the high pressures that are characteristic of injection molding. Combined with lower production costs and no high minimum order quantities, this makes short-run injection molding the ideal choice for companies that need to test their product, prototype, or enter into volatile markets with limited production requirements.
A key advantage of short-run injection molding is its ability to use a wide range of different plastic materials, as opposed to the more restrictive resins used in larger-scale production. The use of different plastics allows for greater flexibility when it comes to testing and developing new designs, ensuring that the final product is perfectly adapted to its environment and specific requirements. This is particularly important for companies entering new or volatile markets, as it can be difficult to predict the long-term performance and durability of a new product.
As a manufacturer that specializes in short-run injection molding, Elimold offers a diverse selection of thermoplastics for use with this manufacturing method. These include high-performance resins such as acetal, nylon, and polycarbonate, as well as general purpose plastics like ABS (acrylonitrile butadiene styrene), PVC, and styrene. All of these plastics can be used in a variety of applications and industries.
In addition to offering a wide selection of thermoplastics, Elimold has no minimum order quantity for short-run injection molding. This means that you can get the plastic components you need without having to pay for a complete set of molds. This makes it easy to test, prototype, and iterate your plastic product while reducing in-house inventory levels and meeting market demand with increased agility.
Long Run Moulding
The injection molding process produces thin-walled plastic parts in a wide range of shapes, including cylindrical, cubic or complex three-dimensional designs. It’s most commonly used to manufacture products like plastic housings for consumer electronics, power tools or automotive interiors. However, it’s also used to make plastic buckets, household products like toothbrushes and toys, and medical devices such as syringes and valves.
The molding process begins by placing a pre-measured amount of molding material into a chamber under heat and pressure, where it is forced into the mold’s cavity. Once the part has cooled, it is removed from the mold. This process can produce parts with intricate designs and tight tolerances, but it’s typically more cost-effective for simple products with consistent cross-sections.
Transfer molding is a good choice for long run production because it uses less heat and pressure to inject the plastic into the mold, which reduces the stress on the machine and mold. It also utilizes a larger passage, called a sprue, which allows the plastic to flow into the mold with less force. This lowers the risk of warping and deformation, but it can also create more noticeable gate marks on the finished product.
In addition to its high level of precision, transfer molding can also accommodate inserts, such as metal prongs or semiconductor chips. These can “float” within the molded plastic, creating components like pins or studs. Combined with a range of finishing techniques, this can give molded plastic components a high-end look and feel.
Another unique advantage of this molding method is that it can be used to create seals with a metal-to-rubber face, which is critical for several industries. For example, natural gas employees use it to create metal-to-rubber seals for their interfaces, and electrical industry workers rely on it to mold connector seals around electrical wires.
Thermoplastics are pliable and can be melted and reshaped multiple times, making them a popular molding choice for disposable items and packaging materials. Thermosetting plastics, on the other hand, cannot be melted and must be solidified once they’re molded, and they are used in more durable applications like electronic components and automotive parts.